How can the pharma industry navigate issues in the global supply chain to minimise drug shortages?
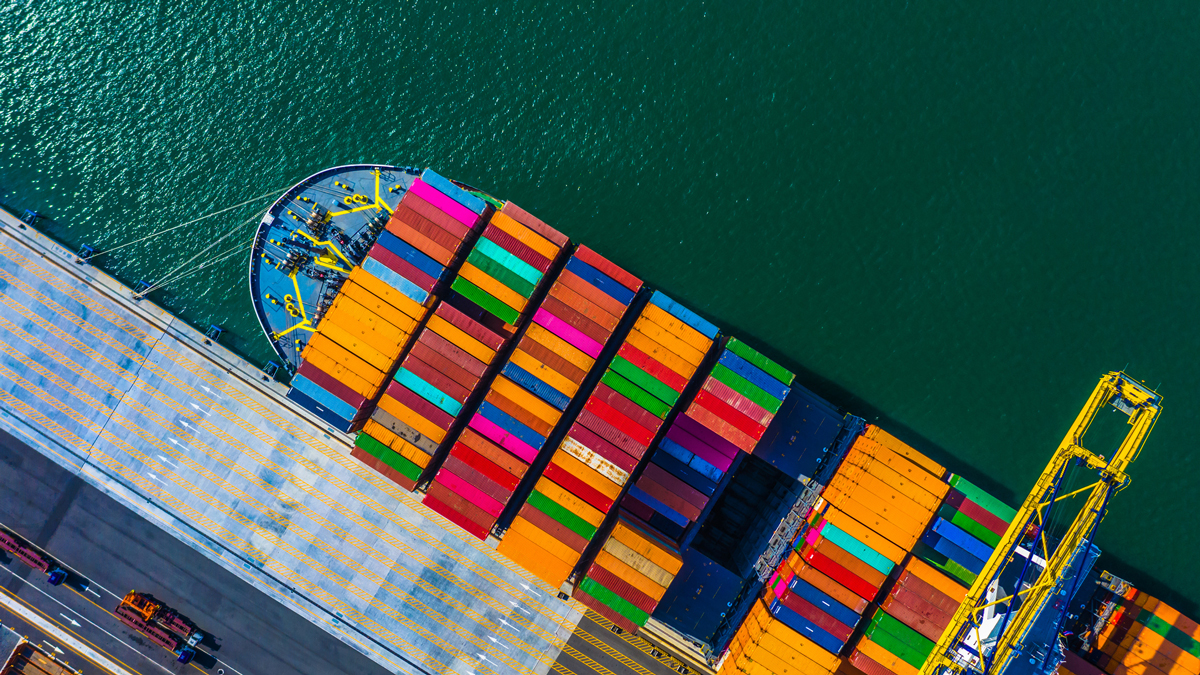
Supply chain shortages have dominated headlines for several months, and the pharma industry has been no exception. While navigating changes has long been a challenge for the industry, the last two years’ events have made supply chain management significantly more difficult.
The pandemic effectively shut down supply chain paths overnight, and as a result, pharmaceutical manufacturers have faced delays and bottlenecks, which have caused drug shortages in healthcare systems. Supply chain challenges are compounded by the broader global picture, such as the war in Ukraine, the great resignation, and natural disasters. These supply chain issues raise significant risks for the industry due to shortcuts being taken that are not based on product safety and quality.
Tackling shortages
Logistical challenges of getting the right materials in the right place remain two years after the pandemic began, causing significant drug shortages to end-users. Businesses are facing challenges in obtaining raw ingredients for medicines.
Many of the medicines most badly affected by these shortages are generic drugs to treat common conditions such as diabetes and heart disease. A break in the supply chain could have enormous implications for millions of people suffering from these conditions.
In the UK, we’ve seen this in the shortage of HRT drugs which has caused ramifications for its users. Given the life-threatening danger of missing out on drugs to treat diabetes and heart diseases, the outcomes could be even worse, demonstrating the importance of businesses overcoming supply chain issues.
So, what can we do to insulate against the risk of shortages in these crucial generic drugs? Above all else, manufacturers need to get their houses in order. That means maintaining regulatory readiness – because having cGMP compliance problems with the FDA can significantly exacerbate the problem.
The FDA can place a foreign company on import alert for cGMP compliance issues in a matter of days – however, it can take a company one to two years to come back into compliance and be reinspected by the FDA. Until the company is found to be in compliance, there will not be a normal distribution of drug products. The stakes are high.
Logistical challenges
With many ingredients shipped in from offshore, businesses need to consider logistics. The two primary exporters of Active Pharmaceutical Ingredients (APIs), China and India, continue to be affected by periodic lockdowns. And while there are occasional discussions about pharma companies re-shoring API production facilities, the process would be extremely expensive and complex.
Companies could benefit from talking to third party experts such as NSF to ensure that they are in compliance. The extraordinary scenario of producing vaccines for a global pandemic led to a well-documented shortage of vials, stoppers, and syringes, and finding a solution is no easy task.
For example, it is no small task for pharma manufacturers to switch out these components, raw materials, and excipients for other components and materials. Compatibility is a real issue, and to replace them wholesale could entail a significant qualification process for the new components and materials.
The same issue, it should be noted, goes for APIs such as Valsartan, the active ingredient in many blood pressure medications. If a company’s submission to the FDA refers only to suppliers from China, it is no small feat to resubmit an application for an alternative supplier elsewhere. It can be done, of course, but it is costly.
Alongside the pandemic and global supply chain issues across all manufacturing, climate change has meant global weather patterns are increasingly volatile and unpredictable. This is placing even more pressure on the transportation of drugs throughout the global supply chain.
The Great Resignation has led to a talent shortage in the pharma industry, just as it has in other sectors, and it is not likely to be over soon. The industry labour shortage ranges from factory workers to qualified staff within the skilled labour sector. This exacerbates the supply chain issue. It is an unavoidable fact that our industry requires a high level of skill and education which makes identifying and hiring talent even more difficult. Meanwhile, attitudes towards work have changed, with a greater demand for work-life balance.
Building supply chain resilience
In a time of uncertainty, companies must ensure that their systems function as intended, have enough resources, and follow the correct procedures. With on-site FDA inspections starting again, it’s imperative that businesses reassess their processes and workforce now to remain compliant. If in doubt, we recommend any business that is unsure about their readiness seek expert consultation and training services, not only for inspection readiness but to help qualify suppliers, deal with and pre-empt manufacturing problems. Many will have former regulators who could prepare businesses through remediation, consultation, mock inspections, gap analyses, and more.
You can check out part 1 of this series, on maintaining GMP readiness, here. Come back next week for the final part, on managing workforce shortages.
About the Author
Maxine Fritz, executive vice president, Pharma Biotech, NSF
Maxine Fritz has 30-plus years of combined FDA, industry and consulting expertise and is responsible for overseeing the pharma biotech practice at NSF International, serving in both a technical and management role. Ms. Fritz works with clients in the pharmaceutical, biologics, biotech and medical device industries to develop quality assurance, manufacturing and regulatory strategies for compliance with FDA regulations. She conducts and oversees regulatory gap analyses, assists with the development and implementation of quality systems, and develops and implements corrective action plans to address deficiencies identified by regulatory agencies. Ms. Fritz has successfully managed, resolved and consulted on large complex compliance projects including corporate warning letters, mass seizure, consent decree(s), Application Integrity Policy (AIP) prosecution and import detentions.
During her tenure with FDA, she was responsible for two consent decrees, multiple warning letters, several new product approvals and three prosecutions. Ms. Fritz received many FDA awards including Investigator of the Year – Los Angeles District, FDA Outstanding Achievement Award, Biologics Team National Award, Crisis Team Management Award and multiple recognition awards. In addition to her FDA experience, Ms. Fritz has worked for the pharmaceutical and biotech industry in management roles leading quality assurance initiatives and activities as well as validation groups and working with manufacturing in variety of dosage forms including sterile aseptic and terminally sterilised parenterals.