Moving to component management & traceability: progress, barriers, and the way forward
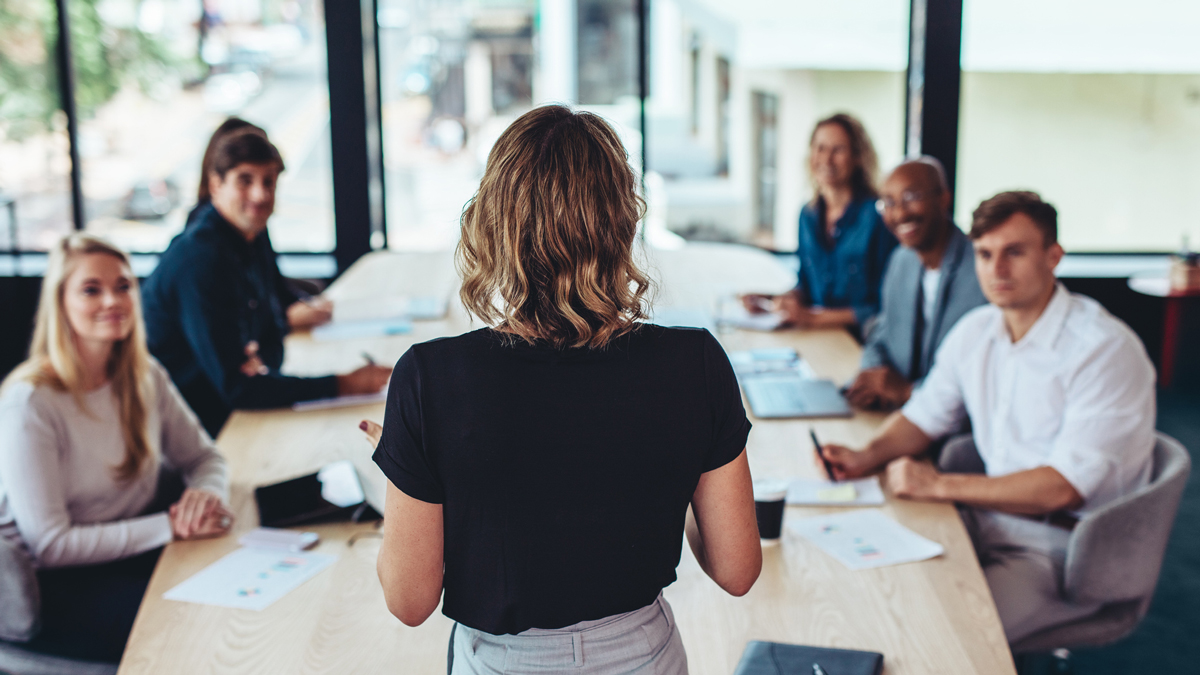
Component management is fairly new to the regulatory market, with pharmaceutical firms moving from traditional document management systems to more dynamic component content management systems. This shift enables companies to improve the quality and compliance of the documents and data that make up regulatory submissions and create a data-sharing ecosystem that enhances healthcare.
Submission status quo
Over the years, pharmaceutical companies seeking product approvals have submitted increasingly vast amounts of information to regulatory agencies. Most of the information is submitted in the form of unstructured PDF documents, with data embedded into them. Regulatory reviewers must then manually ‘mine’ the documents for information, rather than assessing the underlying data used to create the documents.
This situation results in a complex decision-making environment, with high rates of inefficiency, subjectivity, and risk of error. Regulatory agencies are embracing standardized review processes (such as the FDA’s KASA project) that benefit from direct data collection and incorporate review metrics. Pulling data and text from PDFs for standardized reviews is very inefficient, which is where Component Content Management Systems (CCMSs) can improve regulatory submission processes. A better submission strategy uses structured data files and identifiable document components incorporated into regulatory filings, which provide data and information directly to the reviewers.
This new method of data and Component Management enables regulatory review teams to focus on assessing the data instead of the document - a move that promises to deliver positive long-term results.
Reasons for the shift
Aside from the increasing volumes of data, submission teams have other reasons for moving to component management. Tracking where a document has been used does not provide the granularity of information needed for, say, tracking all the places in different documents to different agencies where a new ingredient needs to be addressed. This has to be managed at the data and component level. Life science companies can keep track of where information has been used, re-used, and re-purposed at a very granular level, providing high levels of compliance across all markets and countries.
Building documents from components also reduces review cycle time frames. While some narrative text is still required, auto-population of clinical data into tables eliminates the need for substantial quality control actions. CCMSs also enable and support the harmonization of information, which minimizes the administrative workload involved in receiving, processing, and re-using scientific data across the life science industry.
Key CCMS considerations
Many people consider the difference between document management and component management to be minimal, but there is, in fact, a significant distinction. In component management, handling the many parts of a document – where they are used, where they come from, the separation of text from table data, etc. – becomes a much more complicated operation than in document management. While a single document might only be re-used a couple of times, if at all, components of that document might be re-used a hundred times across multiple applications.
The traceability of components is critical for authoring structured content correctly, especially when it comes to fulfilling compliance regulations. The ability to ensure the correct data is placed into a document table, or the same text is used across similar documents, provides compliance capabilities that are not available at a document level. Coupling data with documents can save hours spent on data quality control for submission documents.
The move to component management has dramatic implications for pharmaceutical manufacturers. Companies increasingly recognize the need to adopt technologies such as artificial intelligence (AI) to assist with this paradigm shift. Using AI-driven programs enables greater traceability of components and improves compliance and efficiencies. As a result, filings and other forms can be completed more quickly and accurately, leading to enhanced quality and regulatory compliance.
Successful CCMS implementation
Implementing a successful shift to a component management system requires companies to overcome several existing barriers. The largest barrier is the perception that all documents must first be broken down into components before using component-based authoring tools. In addition, many document authors seem firmly “married” to Microsoft Word and taking the leap straight to a module-driven component system is too large a step for them, and the absence of sufficient standards for component categorization doesn’t help.
To overcome barriers such as these, it’s necessary to follow best implementation practices. Organizations should continue to use processes and tools already in use, such as Microsoft Word Templates. Within these tools, teams can add fields to the templates that designate re-used information (for example, a generic name, product details, etc.) and automatically populate these fields.
Next, fields within templates for re-used data can be expanded for other information, including tables of data that can automatically be pulled from databases. Finally, metadata can be added to the template to define or outline the multiple components of the document. Some organizations may find that they don’t need to complete this final step and can easily migrate to a CCMS before componentized templates are fully built. However, for most organizations, these steps make it easy to break down Microsoft Word documents into components and feed them into a CCMS.
Mapping the way forward
Making the move from document to component management needs to happen, and it needs to happen now. Companies wanting to get the process underway can start by adopting an approach that continues to use Microsoft Word, at least in the early phases, and provides manageable steps to move from documents to components. It’s important to identify appropriate terminologies to support componentization. Ideally, these should have defined industry standards and controlled vocabularies, however, company standards can be sufficient. They must be able to integrate with (or work across) many types of documents in order to deliver better compliance, more traceability, and easier re-use.
Making it happen
The process starts adding fields to regulatory submission templates that will incorporate re-used information, then building templates with standardized structures and including structured data tags and sources. Fillable metadata is next added to the templates. The full transition comes when authors finally move away from MS Word and start building documents directly from the components.
Making the move towards a full component management system will allow pharmaceutical companies - and the healthcare industry - to become more efficient, reduce costs, and get products to patients faster and more safely.
About the author
Donald Palmer, Senior Director, Regulatory Affairs, IQVIA
As the Senior Regulatory Affairs Director for Business & Technology Transformation, Donald works with the Regulatory Affairs & Drug Development Solutions (RADDS) team at IQVIA to add and update technology solutions to GRA’s business processes. His experience bridges the business and technology divide that spans Regulatory submissions, document management, and Regulatory Information Management, especially as they integrate with other departments and systems. Having worked in several organizations of different sizes, he provides perspectives from sponsors, vendors and now CROs. He is a strong proponent of standards and data governance. With a BA and MA in Mathematics, Donald became fully involved in the pharmaceutical industry just as electronic submissions were starting late in the 1990’s and has over 20 years’ experience in the industry.