How automation can help to address supply chain challenges in pharma
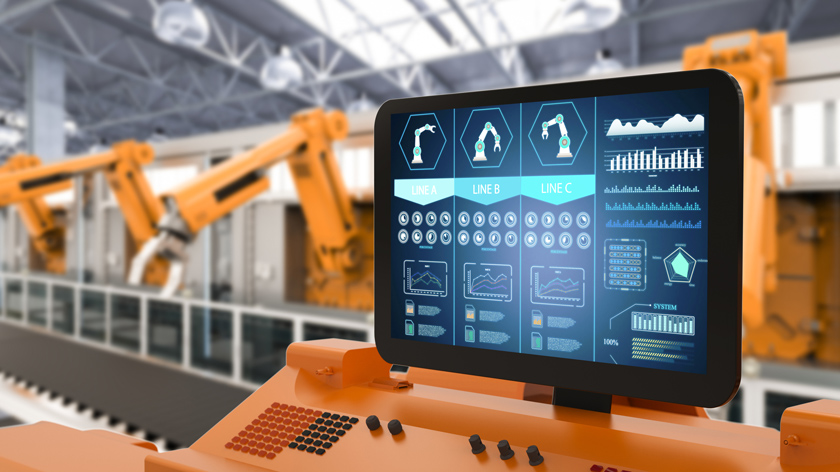
Supply chain issues have been rife in pharmaceuticals for a while, but current socio-economic challenges such as the conflict in Ukraine and the COVID-19 pandemic have led to extended wait times and higher prices for thousands of products. Incidents such as the hormone replacement therapy drug shortage in early 2022 have shown the damaging impact supply chain issues can have on people who depend on these drugs. To combat such challenges, pharmaceutical companies need to adopt processes that are not just efficient, but agile. Automation can be such a solution.
Empowering labs with automated equipment that produces rich, traceable, and actionable data insights means pharmaceutical companies can ensure drug production runs smoothly – even under stress. Modular set ups, remote monitoring systems, and automated batch processing can all assist in helping labs respond to issues as quickly and efficiently as possible.
Supply chain challenges take many forms in pharma – from capacity issues, to managing excess safety stock, and ensuring accurate supplier communication. Here’s how applying automaton in pharmaceutical labs can help address these.
Reducing capacity issues
In recent years, the UK pharmaceutical industry has relied heavily on China and India as providers of active pharmaceutical ingredients. For some products, this results in supply chains that are so complex that they start in Asia and circumnavigate the globe twice, before reaching the final destination. This increase in complexity has left the industry wide open to supply chain shocks from events such as the pandemic, regional conflict, trade disputes, and cyber-attacks.
These shocks can lead to unpredictable or even absent shipments, meaning drug production labs often aren’t dealing with a stable and regular volume of raw materials. When this happens, labs end up working with a production line of either too much or too little capacity, which reduces their efficiency levels, and can result in wasted product.
By moving to a modular automation set up and connecting production line stages with robotics, labs can be more flexible and adapt their equipment to best suit the volume of raw materials coming in. For example, with a smaller shipment, a capping system could be introduced and brought closer to its next step of automated visual inspection, leading to a more efficient production line.
Cutting down on safety stock
Undergoing supply chain issues often causes companies to double down on safety stock, and in a high-volume industry like pharmaceuticals this can get very expensive, inflexible, and often wasteful. Typically, the pharma industry has aimed to increase throughput while maintaining quality, but under supply chain shock conditions this often results in an excessive production of safety stock. This has been the go-to approach for dealing with foreseeable supply chain shocks in the past. However, with a 74% increase in pharmaceutical supply chain disruption in 2021, this approach cannot be sustained for much longer, not only due to the recent pandemic, but to growing geopolitical fragility exacerbating trade disputes and trade routes.
Instead, companies should be looking towards a future where speed and agility are the key components in developing business resilience, rather than a reliance on inventory stockpiles and large quality assured batches.
Automation will be a large part of this long-term vision. Highly exact data monitoring and modular set ups will one day allow production facilities to switch between producing a number of similar products, or alike products that use ingredients from different suppliers in minutes. This means batch sizes can be tailored to daily demands rather than market forecasts.
While these facilities may not yet exist, the principles can be adopted by any pharmaceutical lab by putting more emphasis on agility to help cut down on safety stock. By using automated systems, labs can more accurately and cost effectively forecast the amount of safety stock they will need by not producing an excess amount when they next come under stress.
Better communication with traceable data
It’s imperative that all suppliers and distributors know if disruption is likely to occur, whether that be concerning incoming raw materials or outgoing packaged drugs. The sooner insights can be shared about a potential problem, the better different parts of the chain can react and alter their processes accordingly.
Automated systems allow suppliers to maintain complete traceability over their processes and communicate in the most effective way possible. For example, in a lab, technicians can use software to share their production data in real-time with distributors coming to ship the drugs to market and alerting them to any delays that might occur.
Mix ups in hand-offs are another large disruptor, especially when drugs have specific shipping requirements. For example, many vaccines – including the COVID-19 one – must be kept refrigerated at a specific temperature throughout their journey, and if this isn’t communicated, it can render a whole batch unusable. Fully integrated and automated ingredient to consumer batch tracking using barcoding, RFID tagging, or IoT temperature logging and timestamping significantly reduces the chance of these mix-ups, providing complete traceability records from ingredient manufacturer to patient, and ensures the safety of the product.
End-to-end monitoring for maximum security
Large scale cyber-attacks are becoming increasingly common and are one of the largest and most expensive threats to the pharmaceutical supply chain, with a 2017 attack costing Merck around $425 million. Risks associated with these attacks are significantly increased without a cohesive automation strategy in labs. But implementing a system that provides end-to-end monitoring and integrated information security technologies can help labs become more secure.
For example, by implementing systems that encrypt data straight from the production line, organisations can ensure their data doesn’t leave the lab. However, for this approach to work, it’s essential that automation is embraced at every stage in the process – leaving no gaps for the production to be at risk of an attack.
Closing thoughts
The pharmaceutical supply chain is an important one to keep stable, as many livelihoods depend on it working efficiently. The rapid increase in disruption over the past few years has made it clear that new methods are needed to keep it under control. If disruption continues to occur at the same or similar rate, McKinsey Global Institute estimates that the pharma industry will lose around 24% of one year’s potential earnings before interest, taxes, and depreciation every ten years to cyber-attack alone.
Rather than revert to pushing labs to overproduce safety stock, or outsourcing to even more suppliers causing complex quality and process assurance issues, it is time for automation to be embraced as a long-term solution to dealing with supply chain shocks. Fully automated systems for material handling, combination, and processing offer labs the opportunity to become more agile and better placed to handle and forecast supply chain issues.
About the author
Neil Keegan is head of manufacturing at Automata, a London-based biotech company providing robotic automation solutions to the life sciences industry. Neil leads the manufacturing team, and their work centres on developing and implementing manufacturing and supply chain solutions, alongside Automata’s design team. Neil’s biggest focus is ensuring quality, performance, and excellence at every level of delivery.